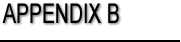
TYPICAL
PROBLEM AREAS
This Guideline was initiated as a result of on-going problems with
the design and construction of Preserved Wood Foundations. Some
of the more common problems related to design and inspection are:
1. Failure to recognize unbalanced backfill loads.
2.
Use of an unqualified inspector to inspect the constructed Preserved
Wood Foundation, with the result that improper construction is accepted.
3.
The significance of the design assumptions in the CSA S406 Standard
and/or the CAN3 086 Standard are not considered or understood.
4.
Failure to prepare and provide a site specific plan.
5.
Inadequate communication between Client and Design Engineer, resulting
in failure to obtain adequate design input information.
6.
Failure to detail special framing, nailing and other requirements
for:
a.
Main floor construction
b. Window openings
c. End wall blocking
d. Stairwell openings
e. Basement floor to wall connection
f. Dropped Floors
g. Racking loads on walls
h. Stepped footings
i. Drainage system
j. Frost protection
7.
Specification of materials that are not available in the market
place.
8.
Details and specifications are not understood or followed during
construction.
9.
Work is covered-up before inspection.
10.
Owners see the engineering requirements as only being needed to
get the necessary permits; once the permits are obtained, the engineered
design is not used for construction.
11.
The Authority having jurisdiction does not require that the Code
requirements relating to engineering of Preserved Wood Foundations
be followed.
12.
Improper backfill material and backfilling procedures.
This list is not intended to include all of the problems that may
exist with the engineering of Preserved Wood Foundations. The Engineer
is responsible to ensure that the engineering services provided
on Preserved Wood Foundations comply with all of the relevant codes,
standards and the intent of this Guideline.
|